Potting is an essential process in the precision electronics manufacturing industry. As many industries such as automotive electronics, photovoltaics, and aerospace enter a period of rapid development, the automotive electronics industry is becoming more intelligent and electrified, and vehicle controllers,
The demand for automotive electronics such as motor controllers and battery management systems continues to rise. Solving the bubble problem in potting materials has become a key to manufacturing high-yield products!
PART.01 Causes of bubbles
Whether it is electronic components such as sensors and high-end chips, or production links such as solar cell production and photovoltaic power generation group packaging, they are all inseparable from the requirements for the potting process.
If bubbles are generated during the potting process, it will cause greatly impaired the performance and service life of the material.
Why do air bubbles form in potting materials? There are three reasons.
1. When the shape of the product parts is complex and the potting space is narrow, during the production process, the potting material cannot fill all the internal gaps. The air, water vapor in the atmosphere and the moisture on the product surface are not discharged in time and are compressed by the glue.
It reacts with glue to form crystals, which can cause bubbles to form in the residue.
2. If the potting machine is operated improperly, the glue dispensing speed is too fast or too slow, and the glue viscosity is too high or too low, bubbles will form when glue splashes on the potting surface during the potting process.
3. On the market, some low-end equipment pre-treats the potting material and supplies it to the dispensing head. Due to the limitation of the function of the glue booster of the low-end equipment, the preparation unit cannot supply the glue to the dispensing head in a vacuum environment, so that it retreats to the atmospheric environment, and the glue will form bubbles, and if the preparation unit of this type of equipment does not have an internal circulation system for the glue, the pipeline will also produce air bubbles.
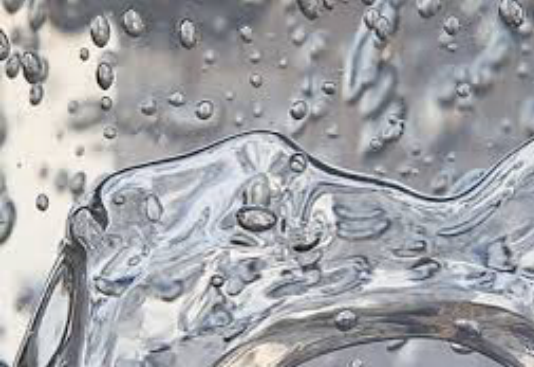
Bubbles in glue under microscopic lens
PART.02 Serious consequences caused by air bubbles
Never underestimate the dangers of air bubbles. The occurrence of air bubbles during the glue preparation and potting process will have a variety of negative effects on the performance of the potted colloid.
First of all, bubbles will cause uneven pressure distribution inside the colloid and excessive local pressure, causing the colloid to expand or deform due to the high and low temperatures and high and low pressures of the external environment during use,
eventually leading to component damage and outer layer cracking. .
Secondly, bubbles will reduce the sealing performance of the glue, resulting the internal connection of the glue-filled body to be unstable, accelerating the oxidation and corrosion of its parts, and thus affecting the overall performance and lifespan.
For example, the amine curing agent in the epoxy resin curing agent, even if it is exposed to the air for a short time, will absorb moisture and react with water vapor to reduce the activity of the curing agent and produce many honeycomb pores,
which will make the potting colloid to reduce the strength, durability and lead to the end of life.
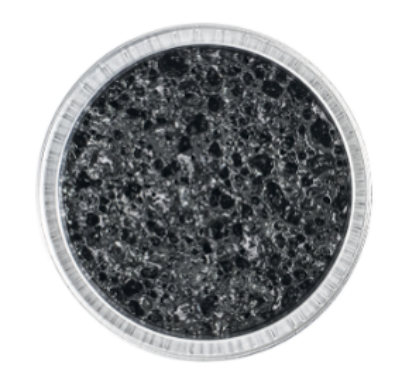
Honeycomb pores produced after epoxy resin absorbs moisture
Especially for electronic components, the presence of bubbles will make the local electric field distribution uneven, leading to a decrease in local insulation capabilities, thereby reducing the insulation performance of the entire potted colloid, causing the potted colloid to be scrapped due to local short circuit very quickly during use ( Such as ignition coil, transformer, etc.). Therefore, in the manufacturing process of electronic components, it is necessary to use homogeneous, bubble-free potting materials and strict process control to ensure the effective potting of the product.
Increasingly stringent quality control and workpiece complexity have put forward higher requirements for bubble-free potting. So how does MEST solve this problem?
The G380 vacuum material preparation & feeding system independently developed by MEST performs glue pretreatment actions such as heating and stirring the glue, circulating the vacuum pipeline, etc., which can ensure the vacuum environment of the glue during material preparation and pressurized supply, and isolate air moisture.
Vacuum potting prevents air or water vapour from mixing with the product during the potting process and allows the glue to permeate the entire body without bubbles. MEST's vacuum potting system ensures an airtight vacuum environment from the preparation of the material to the supply of the material for the potting process,
avoiding the generation of air bubbles.
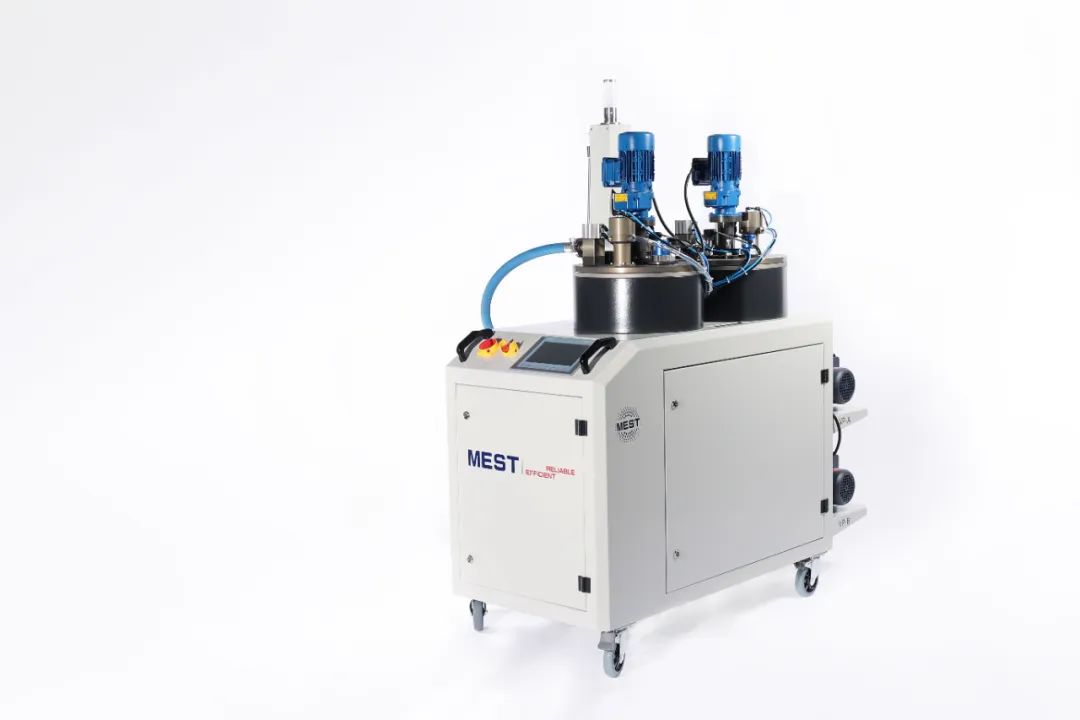
MEST - G380 vacuum material preparation&feeding system (suitable for self-leveling glues such as epoxy resin, polyurethane, silicone, etc.)
After completing the material preparation, the vacuum glue injection station MEST-GV series strictly ensures the vacuum operating environment,
places the potting material in the vacuum, and sends the potting material to the piston glue injection valve MEST-P20 by the stacked three-axis for high-precision and controllable Convenient dispensing operation.
During this process, we will use relevant processes to ensure that the glue is completely pushed into the internal gaps of the colloid.
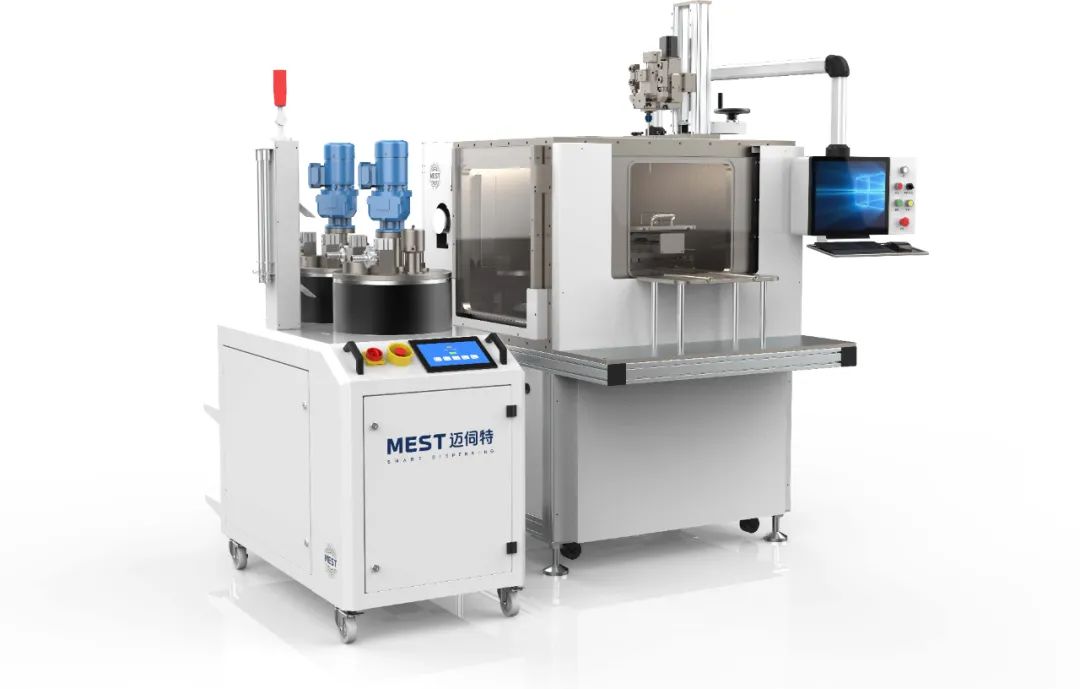
MEST vacuum series products: vacuum injection station GV334, vacuum material preparation&feeding system G380, piston injection head P20.
Conclusion
CITIC Securities research report pointed out that in the trend of medical device segmentation industry, upstream core components and some high-end parts are still mainly supplied by imports.
There are high barriers to some high-end core parts in CT and other fields, and in the production of these core parts In structures, vacuum potting technology is usually required to ensure precise positioning and stable connections. At the same time, this also helps protect components from vibration and impact, improves equipment reliability and stability, and extends service life.
MEST's vacuum potting system ensures bubble-free, high-quality potting results. On the one hand, MEST can customize products in advance according to customer products, so that every customer can find the most suitable solution; on the other hand, for consumer electronics, new energy vehicles, medical devices, etc., where the product iteration is fast and varied. MEST will also flexibly adjust the structure and functions of dispensing equipment to meet the needs of customers and products in different industries.
In the future, based on the service concept of "Making Dispensing Easier", MEST will continue to deepen the independent research and development innovation, and bring more high-quality and high-precision dispensing solutions to customers, so as to make the dispensing manufacturing have more possibilities.