As an expert in precision fluid application control, MEST relies on its rich development experience and innovative ideas to continuously explore more efficient and reliable dispensing solutions. Today, we will talk with the R&D engineers about the high-end series product of MEST, the vacuum preparation&feeding system G380, and the highlights of this machine in terms of functions, applications, etc.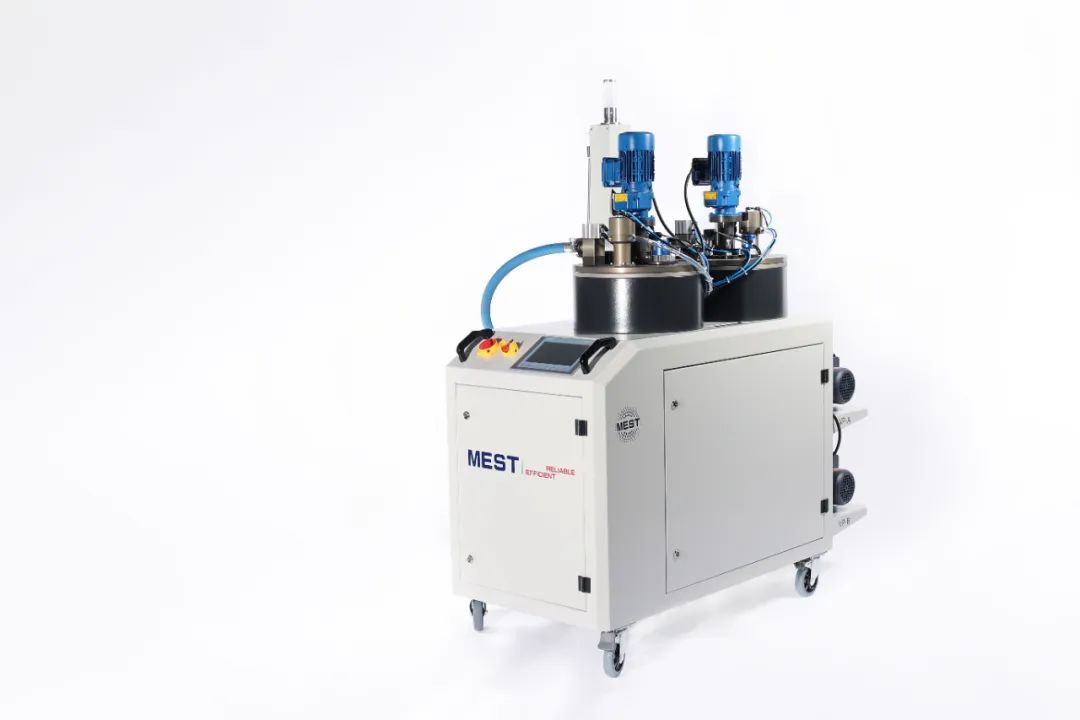
Q1:Please briefly introduce the G380 and what is the biggest difference between it and our classic C5 series, V series, and T series?
A:From new energy automotive electronics, photovoltaic solar energy to aerospace and other industries, if there is a lack of effective and reliable adhesives and potting processes, their products or components will quickly fail. G380 is a product that can highly meet specific potting and injection needs.
G380 can be applied to any single or two-component silicone, epoxy resin, polyurethane vacuum preparation needs that can be automatically leveled in heated or non-heated environments; in high vacuum (can be completely close to absolute vacuum), fully controllable Under temperature and uniform stirring, G380 can make the glue flow back and forth in the equipment to ensure that the density of the glue is completely uniform and bubble-free, so that all quantitative valve bodies it connects can achieve better dispensing and potting effects.
The biggest difference between the G380 and MEST's classic dispensing equipment such as C5 and V4 is that the G380 is a glue supply and preparation unit, not a dispensing system. Its glue injection operation needs to be combined with the P20 dispensing head independently developed by Mystor. Or realize it together with C30 and GV series of vacuum injection stations.
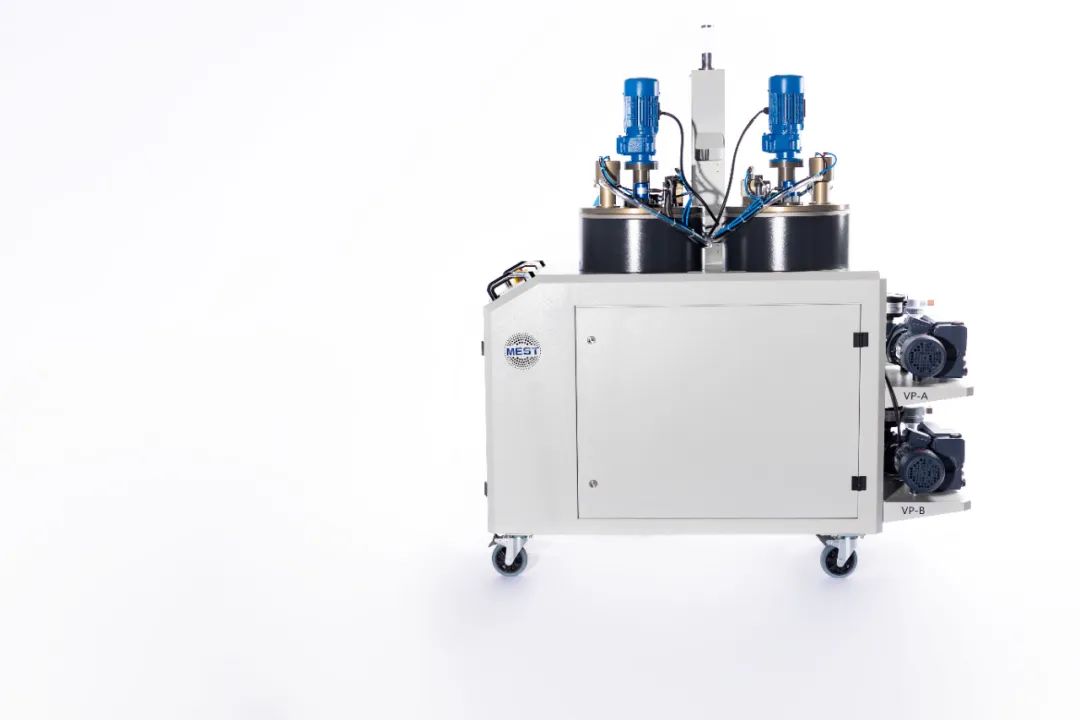
Q2:What situations require material preparation and supply in a vacuum environment?
A: For example, when dealing with sensitive materials that easily react with water vapor or need to be prepared in a vacuum, this type of glue will react with the atmosphere to produce bubbles and crystals once opened. Glues with bubbles or crystals will cause the product to quickly fail or fail after mixing. scrapped. In order to avoid such a situation, it is necessary to store the glue in a vacuum environment and ensure that the density of the glue is uniform. In the G380, a fully sealed vacuum environment can be ensured from the material preparation unit to the conveying pipeline, completely avoiding all factors that affect bubbles in the glue.
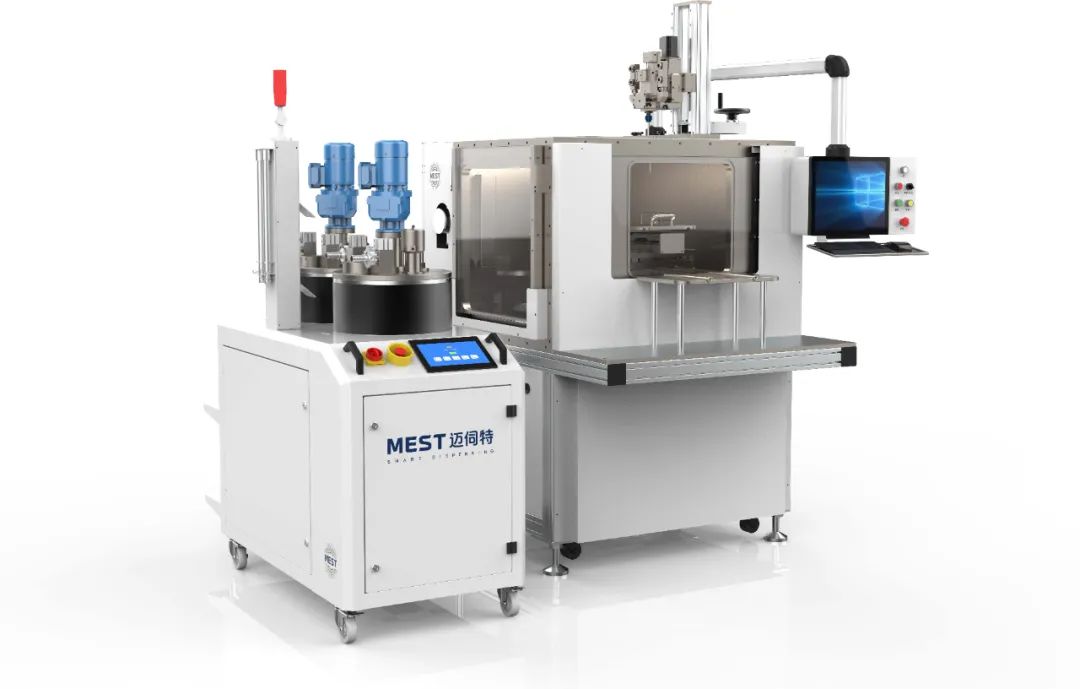
▲ Mesote vacuum material preparation solution
The picture above is our G380 vacuum material preparation solution. This solution has the advantages of high vacuum, no downtime, modularity, user-friendliness, and durability, and is widely used in various industries.
Q3:Can you give us some examples of the application of G380 in dispensing?
A:Ignition coils, tire pressure detection sensors, multimedia systems (navigation, audio, etc.), photovoltaic circuit boards, etc. on cars all have extremely high requirements for glue pretreatment. For example, wevo pu403fl glue, which is widely used in the field of automotive electronics, is an automotive electronic potting glue that is very sensitive to water vapor. Its maximum temperature resistance is 165 degrees, its Shore hardness is only D40-50, and its anti-seismic coefficient is high. Therefore, it also has very high requirements for glue processing equipment, and G380 can well meet the glue processing needs of wevo pu403fl.
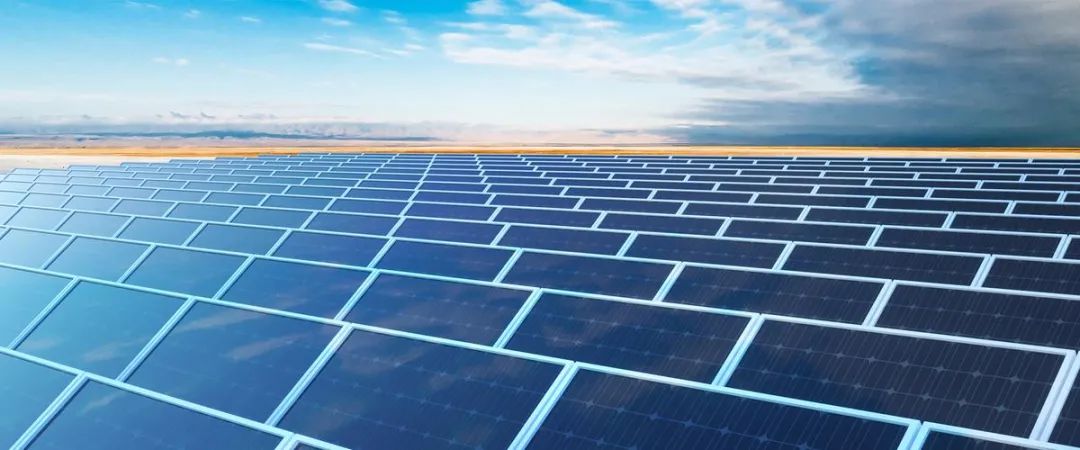
▲ Photovoltaic circuit board
Other fields, such as consumer electronics (mobile phones/computers/tablets), home appliances (washing machines/refrigerators), municipal lighting, aerospace, deep sea navigation, military industry... As long as there are electronic products with weather resistance requirements, G380 can be used to solve them.
Q4:How does the G380 ensure a vacuum environment during development and manufacturing?
A: We strictly control the research and development, parts procurement, assembly, debugging and other aspects of the machine. When assembling the equipment, use precision machined parts to assemble the equipment. For the parts and connections that need to be sealed, use O-rings, thread sealants, flat sealants, oil seals, skeleton seals, etc. that will not react chemically with the adhesive. Ensure that the equipment hardware is well sealed; before the equipment leaves the factory, the vacuum leakage amount is simulated in a vacuum environment of about 2mbar. After the leakage amount reaches the standard, it is installed into the material preparation and circulation functions of the customer's glue testing equipment. In addition, according to the physical and chemical properties of different glues, the viscosity can be adjusted by heating to increase the flow rate of the glue and improve the dispensing effect.
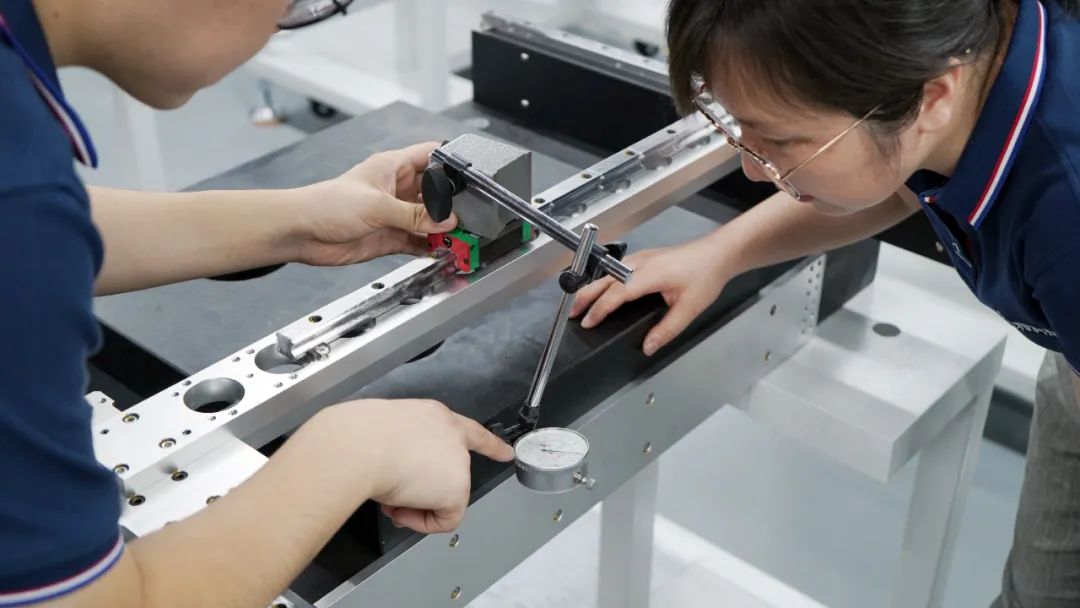
Q5:For such a high-end and precise machine, what kind of guarantee can we give our customers in terms of after-sales service?
A:We implement one-stop supply in production and produce spare parts independently to flexibly respond to spare parts replacement needs. The professional after-sales service team responds 24 hours a day to ensure users’ purchasing experience.
Q6:Okay, besides G380, what other products can meet special dispensing needs?
A:In addition to G380, we also have single and double-component filling and dispensing systems such as vacuum low-pressure plate pump G280 and vacuum glue injection station GV series, which can meet special high-demand dispensing processes according to user needs. In the future, we will continue to launch new products that meet the development of market demand, and we will share them with everyone in the future!